Growing up in a construction family in the Northeast — oftentimes, jobsites were my playgrounds — has given me a different perspective when tackling termite work. Regardless of what state you’re in, building construction types, ever-changing building codes and so-called standard practices (such as burying wood cuts and other cellulose debris rather than hauling it offsite) all can have an impact on your termite treatments. Understanding basic building construction and slab types is becoming more important when ensuring your treatments provide the results you’re looking for: a termite-free structure.
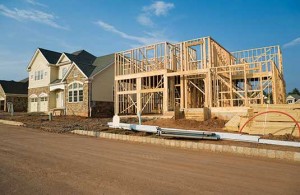
Understanding basic building construction and slab types is important when ensuring your treatments create a termite-free structure.
First things first
When we contemplate termite work, we think about a number of things: termite species; inspection techniques; inspection equipment; geography; soil type; tools needed, including product(s), etc. Do we also take a moment to think about construction types, the different issues with the differing construction methods, and whether additions have been made to the original structure? Questions we should ask about subterranean termites include:
•
Is this really the footer, or just concrete overpour?
•
Will we need to drill extensively?
•
Are there abutting slabs or cold joints, and if so, how do we handle them?
•
Which product or combination of products should I choose?
There are no cookie-cutter answers to these questions. Every termite job is different, and your approach to termite work should include asking yourself all of these questions and maybe even more, depending on your local geography, nearby bodies of water, and state requirements and restrictions.
Beyond the facade
Just as termites are cryptic creatures, many construction issues can be hidden from initial view. They require thorough inspections combined with multiple questions for the homeowner to answer, especially about any and all structural modifications that have been made to a structure. You’ll find that much of the time, the structure has changed hands; the current owner might not have the original blueprints or even know what the original footprint of the home looked like.
This is where we have to be open to in-depth discussions and asking as many questions as it takes to make sure you can provide the best treatment possible for your customer. After all, you’ll more than likely be offering a warranty on your work, and doing the best job possible is good for your customer, you and your business.
It’s good to have options
Control Solutions Inc. offers many choices when it comes to termite control. Whether you prefer repellent or non-repellent options, we have you covered. We’ve recently expanded your options for termite control with the launch of FUSE Termiticide/Insecticide. We’re excited to offer FUSE, which features two non-repellent, non-pyrethroid active ingredients: imidacloprid and fipronil. FUSE is labeled for termite applications, as well as ant and perimeter pest management. Be sure to check out all of our products at ControlSolutionsInc.com — and please, always read and follow label directions.
At CSI, our driving mission is to develop effective, sustainable and economical pest control formulations that improve the results (and the income potential) for the PMPs who use them.
PS: Don’t believe what you hear. There’s a lot of wood involved in concrete block and steel frame construction.
Marie Knox is PCO technical manager, product development, Control Solutions Inc. She can be reached at mknox@controlsolutionsinc.com.
Leave A Comment