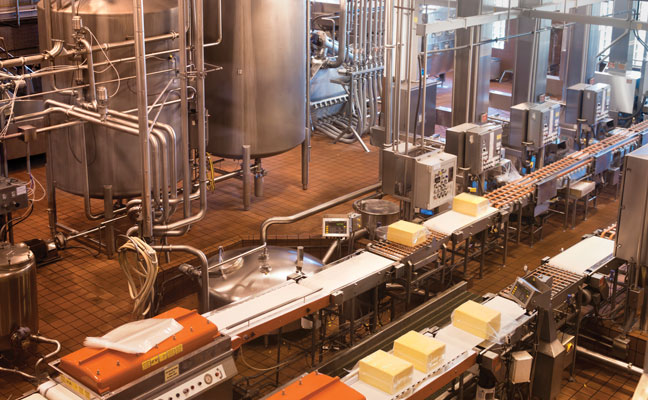
PHOTO: LEEZSNOW/E+/GETTY IMAGES
I’d wager that today, about 50 percent of food plants have outside professional pest management providers, and 50 percent have in-house service. For pest management professionals (PMPs) who can land such accounts, the food-processing industry usually is stable, and offers year-round work.
It takes some thought and planning to get into this service segment, however. One misconception is that if you can service your local pizza place, you can service a food plant. It’s a little more complex than that.
The food processing industry has formal systems in place, from good manufacturing practices (GMPs) to pest management tracking. The first goal is to understand the needs of the customer, and then to be prepared to implement those programs. A discussion with potential customers should include their expectations, frequencies, the values of the partnership, and even the history of pests in their facilities.
THE TECHNICIAN IS THE FACE OF THE COMPANY
Some companies are shifting toward universal technicians, who handle both residential and commercial accounts. If they’re handling eight or more stops a day, this may not be a good fit. A food plant technician must be knowledgeable, meticulous, and fully aware there could be hundreds of food plant employees watching his or her every move. There’s no hurrying around so the tech can make it to the next appointment on time. Rather, the plant needs a partner it can depend on for expertise and thoroughness.
In addition, food plants are very sensitive to security, and communicating with the proper personnel can be hard to do. The best way to break down that barrier is to have you as the owner (and even the technician) join and actively participate in food industry programs and trade associations. For example, the Association of Food and Drug Officials, online at AFDO.org, was started by a group of relevant government agencies and today, industry members are active participants as well. Engaging in these groups will give visibility. You’ll get to know the players, and you’ll meet food industry decision-makers you might not normally encounter.
Further, these groups discuss tough issues and work on solutions together. While it might take some time, participation will pay great dividends. As a former food industry quality assurance director for a very large company, I can say that when we needed an outside pest management firm, we always looked first to pest management firms we met through these organizations.
TOOLS IN THE TOOLKIT
A few simple tools are necessary to service any food plant. This list is just a start — and even if you don’t end up servicing food plants, it is still a good checklist for any technician to consider.
⦁ Recordkeeping available 24/7/365. When a customer complaint comes in, the client will want to see the records for that plant ASAP. Whether it’s digital or in a book, this is a vital component.
⦁ A strong, rechargeable flashlight. About 90 percent of your service time will be spent on inspection. You want a main flashlight, and a backup should anything go wrong with it.
⦁ Kneepads. Kneeling on quarry tile for years eventually will become painful, and pads can help protect your knees.
⦁ Hand lens. It can be small and inexpensive, but a hand lens will greatly help identify pests onsite.
⦁ Small plastic bags with labels. These will allow specimen collection, and the ability to record where the specimens were collected.
⦁ A mechanic’s mirror on an extension. You need to look under and behind all equipment to find the source of any infestation or potential infestation.
⦁ Icing spatula (modified). To pull out spilled food under equipment, buy a tapered, offset icing spatula from any baking supply house, and bend the metal tip up with pliers to about 30°. Speaking from experience, you will be able to collect samples and probe spilled food for insects without scraping your knuckles.
BAUMANN, a PMP Hall of Famer (Class of 2013), is VP of technical services and regulatory affairs for Nisus Corp., Rockford, Tenn. He can be reached at gregb@nisuscorp.com.
Leave A Comment