By Andrew Greess
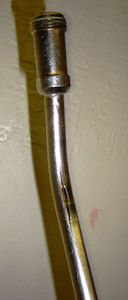
This compressed air sprayer wand has freeze damage that resulted when the pressure was not released from the system.
Pressure is good. Without it, most power and manual pest management sprayers won’t work. The problem is too much pressure, which has a number of negative impacts — including decreased sprayer life.
Here is an interesting observation: When we build a new gas-powered pest spray rig, we set it at about 75 psi. When spray rigs come into our shop for service, they are often set at 150 psi or higher.
The pressure isn’t magically increased by a pressure fairy. Pest control technicians turn up the pressure to finish their jobs faster. Here are some of the consequences of running a power sprayer at higher pressures:
- Higher operating pressure reduces the life of the pump, hoses, fittings, o-rings, seals, gaskets, etc.
- Chemical spills will be larger and more serious when a component bursts at higher (rather than lower) pressure
- Higher pressure can also affect spray droplet size, which can cause unintended consequences such as spray drift. (Can you say “lawsuit”?)
How do you prevent such a situation from occurring? My suggestions include:
- Set a company policy for proper power sprayer operating pressure.
- Train technicians to operate power sprayers at the recommended pressure.
- Have your supervisors regularly check the operating pressure when observing technicians in the field.
- Start up the power sprayer and check its pressure as part of your regular vehicle inspection.
Overpressuring can damage manual sprayers, such as backpack sprayers or 1-gal. compressed air sprayers. The most common problem we see is that when a manual sprayer has a problem, technicians will try to work around it by overpressuring the sprayer. This doesn’t solve the problem; it just inflicts more damage on the sprayer — which will now require more expensive repairs.
Another great way to reduce spray equipment problems is to release the pressure on your (power or manual) sprayer after each stop to prevent problems. Release the pressure by squeezing the spray gun handle to let the pressure drop in the line. The power sprayer must be turned off, and the manual sprayer must not be pumped up. If spraying extra chemical on the ground is a problem, open the lid of the sprayer tank and spray the product back into the tank.
Releasing the pressure on the sprayer extends the life of soft parts like hose, o-rings, gaskets, etc. We used to suggest releasing the pressure at the end of each workday, but technicians forget and sprayers end up stored under pressure all night. Remember, summer temperatures on the truck are higher than ambient temperature, so the pressure in your system will increase if you don’t release the pressure.
Releasing the pressure also reduces the chance of freeze damage should a deep freeze occur. If the sprayer is stored under pressure and the temperature drops, there is nowhere for the water to expand. The weakest link in the system will break when the water freezes.
Train technicians to release pressure of all power and manual compressed air sprayers at the end of each stop to extend the life of your equipment, and reduce breakdowns and downtime.
Leave A Comment